In industries where precision, cleanliness, and efficiency are critical, non-contact dispensing has emerged as a game-changer for fluid control. Whether it’s in electronics manufacturing, automotive assembly, medical device production, or even pharmaceuticals, this advanced dispensing method offers a clean, accurate, and highly repeatable way to apply fluids without physically touching the substrate.
Unlike traditional contact-based methods that rely on needles, syringes, or nozzles making direct contact with a surface, non-contact fluid dispensing uses high-speed valves, piezoelectric actuators, or jetting systems to “shoot” or eject tiny amounts of fluid from a distance. The result? More control, less waste, and minimal contamination risk.
What Is Non-Contact Fluid Dispensing?
Non-contact dispensing refers to the precise application of liquids, adhesives, or coatings onto a surface without direct contact between the dispensing nozzle and the target material. This method uses technologies such as:
- Piezoelectric jetting valves
- Time-pressure systems
- Electromagnetic actuators
- Pneumatic or solenoid-based systems
These systems are capable of dispensing micro-droplets or continuous streams of fluid at high speed and with micrometer-level accuracy.

Key Benefits of Non-Contact Dispensing
1. Precision and Repeatability
One of the greatest advantages of non-contact fluid dispensing is its high degree of accuracy and repeatability. The systems are capable of delivering exact amounts of fluid in micro to nano-liter volumes with consistent results, which is essential in industries like microelectronics and biotechnology where tolerances are tight.
2. No Surface Damage
Because there’s no physical contact, there is no risk of damaging delicate or uneven surfaces. This is particularly useful when working with sensitive components such as printed circuit boards (PCBs), wafers, or fragile medical devices where even light pressure can cause harm.
3. Reduced Risk of Contamination
In contact dispensing, the nozzle or needle can pick up contaminants or particles from one surface and transfer them to the next. Non-contact systems eliminate this risk, making them ideal for cleanroom environments and sterile applications.
4. Higher Throughput
Non-contact dispensing systems can operate at high speeds, making them suitable for automated production lines where speed and precision must go hand in hand. This increases throughput and reduces downtime caused by clogging or manual adjustments common in traditional methods.
5. Greater Flexibility in Design
Because the dispensing head doesn’t have to touch the surface, manufacturers can apply fluids in hard-to-reach areas, curved surfaces, or 3D-printed parts with varying geometries. This opens the door to more innovative product designs without compromising production efficiency.
6. Minimized Waste and Cost
With better control over the amount of fluid dispensed, manufacturers can reduce material waste, especially with expensive adhesives, coatings, or biologics. This also means lower operating costs over time and more sustainable manufacturing practices.
7. Easy Integration with Automation
Modern non-contact dispensing systems can be seamlessly integrated with robotic arms, conveyors, and vision systems. This makes them ideal for Industry 4.0 environments, where smart manufacturing and real-time quality control are priorities.
Applications of Non-Contact Fluid Dispensing
Non-contact dispensing is revolutionizing fluid control in a wide range of industries:
- Electronics: Applying solder paste, flux, and adhesives to PCBs with high precision.
- Medical Devices: Dispensing small volumes of reagents or adhesives without contamination.
- Automotive: Sealing or bonding parts with consistent application and reduced mess.
- Pharmaceuticals: Accurately dispensing medications, serums, or active ingredients into vials or onto packaging.
- Consumer Goods: Labeling, packaging, and bonding parts quickly and cleanly.
Each of these use cases benefits from the control and efficiency that non-contact dispensing systems provide.
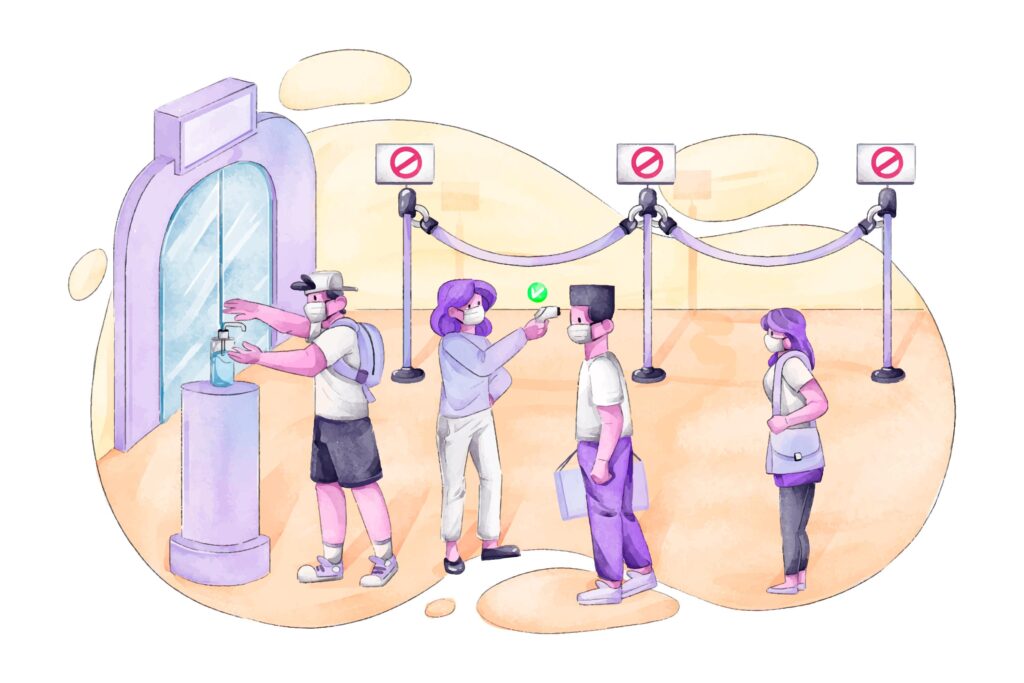
Challenges and Considerations
While non-contact dispensing offers many benefits, it’s not without its challenges. Factors like fluid viscosity, temperature sensitivity, and substrate material can affect performance. Choosing the right dispensing technology and calibrating it properly is essential for optimal results.
Additionally, regular maintenance and calibration of the dispensing system ensure continued precision and reliability over time. Working with a trusted supplier or system integrator can help tailor the right solution for your specific application.
Final Thoughts
Non-contact dispensing represents a significant leap forward in fluid control—offering unmatched precision, cleanliness, and versatility across a range of industries. As manufacturing becomes increasingly automated and specialized, the demand for efficient, touch-free, and contamination-free fluid application methods will only continue to grow.
By adopting non-contact fluid dispensing, companies can improve product quality, reduce waste, and streamline production processes—all while maintaining the integrity of sensitive materials and surfaces. In today’s fast-paced manufacturing environment, that level of control isn’t just a benefit—it’s a competitive advantage.